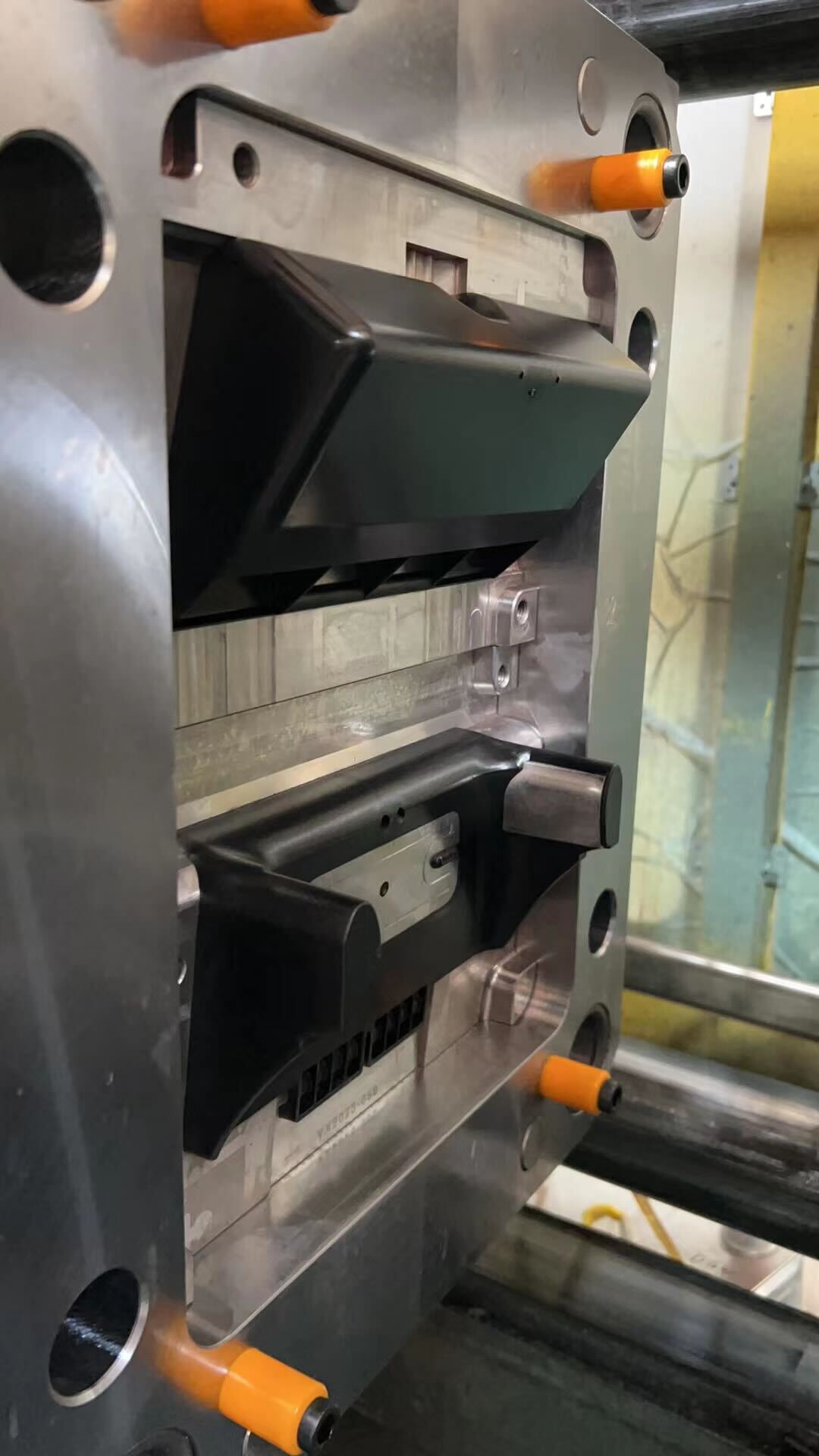
Blog 12: Molds nearly complete and timeline update
Share
Hello Everyone,
Exciting developments are underway in our mold production, and we're eager to share our progress with you. The molds are nearing completion, and we've successfully crafted some prototype parts using a cutting-edge plastic injection molding system.
This is the mold for the upper body and the tray.
These are all the parts together, but not finalized. The texture and the color are not locked in.
This is the underside of the sunglass holder
The sunglass holder parts are sitting inside the mold
This is the picture of the sunglass holder mold in the injection molding machine
This is the negative cavity of the mold. You can see the intricate details of how everything fit together.
Plastic injection molding is the innovative technique at the heart of our manufacturing process. In essence, it involves injecting molten plastic into meticulously designed molds to produce precise and high-quality parts.
Our molds, each weighing hundreds of pounds, are meticulously carved from large blocks of metal. The intricate development process demands extensive hours and deep expertise to ensure precision and functionality. These molds play a crucial role in shaping the final products, and we are committed to delivering excellence in every detail.
The upcoming steps involve creating the actual parts and finalizing the assembly. To guarantee the dimensions meet our expectations, we'll employ a Coordinate Measuring Machine (CMM) to measure individual parts. This meticulous process ensures the molds and parts are crafted with the utmost accuracy. Following this, we'll conduct thorough testing to validate that the parts perform as designed.
Once we confirm the fitment and functionality, our focus will shift to refining the color and texture of the parts to seamlessly match the Tesla interior.
Here's a timeline outlining the key steps in our production process:
- Finalize molds geometry - Completed
- Measure the part using the CMM machine
- Assemble the part - 4 days
- Verify functionality and check for defects - 2 days
- Develop assembly procedures and initiate team training - 1 week
- Ship the sunglass holder from China to DockCharged for approval and testing - 1 week
- Order raw materials and boxes for manufacturing - 3 days
- Commence the manufacturing process - 15 days
- Load batches onto sea shipping boat and deliver to DockCharged for distribution - 30 days
We estimate that the parts will arrive in late January and then we will begin shipping.
DockCharged EV charger
If you have a friend, loved one, or family member that has difficulties charging in their apartment or condo... or home where they can't easily install 220V (L2 Charging), then please let them know about DockCharged. Our charger, launching soon, allows them to Level 2 charge but without any installation cost.
We use batteries and software to fast charge a car. While you're away from home, the Dockcharged stores energy into it's batteries, then rapidly deploys the energy back into the car and, in parallel, sends power from the wall into the car too.
www.Dockcharged.com
We appreciate your continued interest and support as we strive to deliver top-notch products.
Best regards,
Doug, Javier, Chris, Cristian